
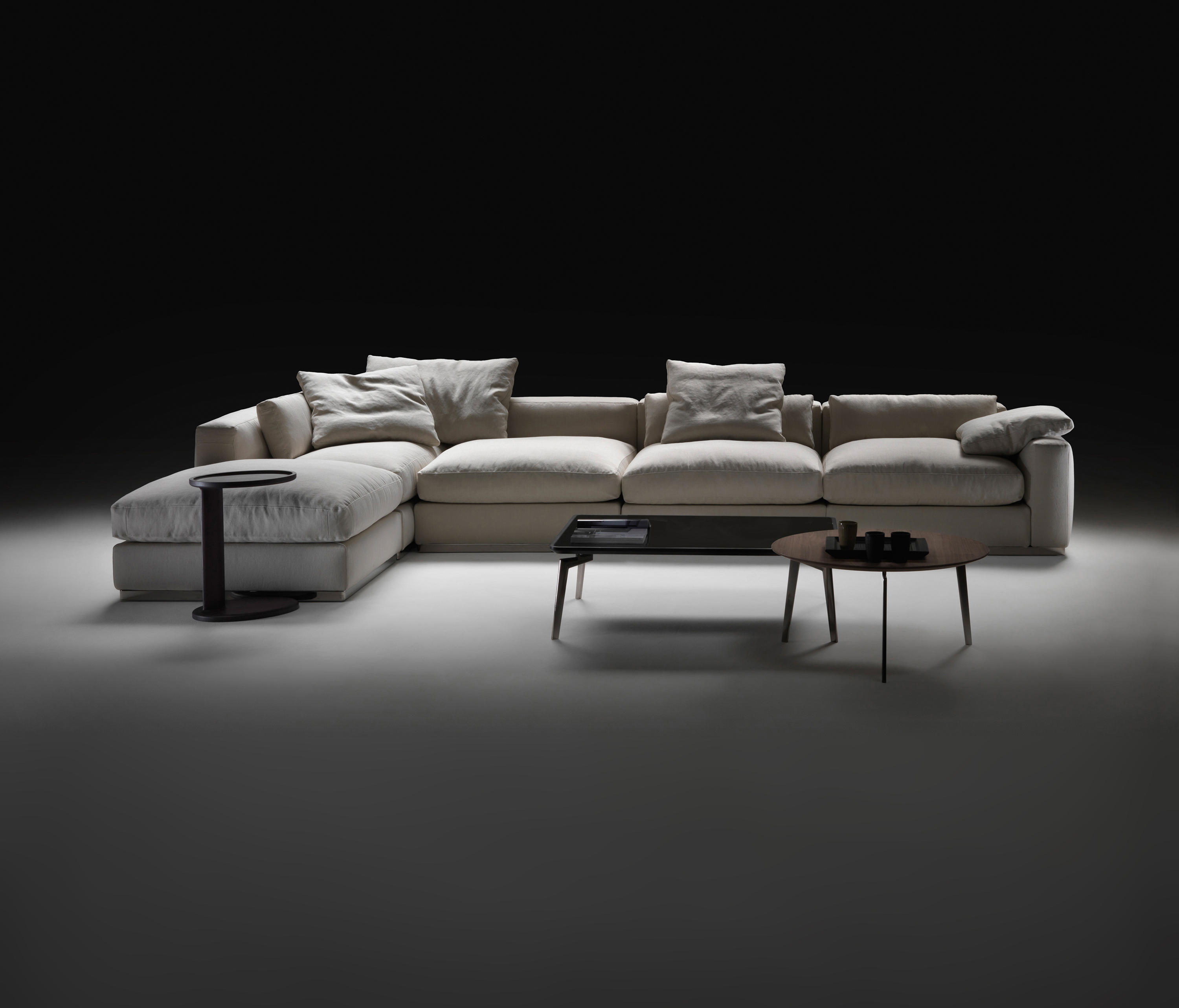
Numerically, the iterations may not converge because the failure jumps back and forth between the two layers. In the mathematical model, however, both layers fail simultaneously. We cannot predict which layer will fail, since that is controlled by manufacturing inaccuracies. The slightly stronger layer will then be unloaded as the force through the part decreases. In real life, one glue layer will fail before the other.

When this happens, the surrounding material is unloaded.Ĭonsider this example of three elastic blocks joined by two glue layers:
Flexture design crack#
When increasing the load, a crack will form at the location with the lowest strength, even if the stress state is homogeneous. In a physical material, the strength does not have a perfectly uniform distribution. With softening material models, it is extremely difficult to achieve convergence in a finite element model if the stress state is homogeneous. The longest test specimen in the experiments was 26 meters and occupied a large portion of the lab! The experiment was reported in the article “The stability of very long bend specimens” in the International Journal of Pressure Vessels and Piping. The tests highlighted that crack stability is not only a function of the local stress state, but also of the capacity that the stored energy in the test specimen has to drive crack propagation. Years ago, a friend of mine at the Department of Solid Mechanics at KTH Royal Institute of Technology in Stockholm performed some interesting experiments where he studied the stability of cracks in a ductile steel using extremely long three-point bend test specimens. If, for a certain incremental displacement \Delta u_1, the energy released by the elastic parts is larger than the work needed to produce the same displacement in the cracking part, the state is unstable. The only way the energy can be absorbed is by doing work on the damaged part. This means that elastic energy is released. If the external displacement remains fixed, then the elastic parts of the structure must contract to compensate. The damaged part of a structure elongates while its force decreases. The energy dissipation and the displacement (or strain) at final failure have a physical meaning. The area under the triangular force-displacement curve in the material model represents the energy dissipated by the process.
Flexture design free#
In reality, we are not free to make arbitrary choices about force and stiffness. The force in the lower branch is independent of damage:Ī globally stable system (left) and a system where the stiffness in the lower branch is too small to maintain stability (right). The peak force F m is reached at the displacement u m. The material model for the first spring is bilinear. The spring k 1 represents the material with the damage model, whereas the other two springs are purely elastic.
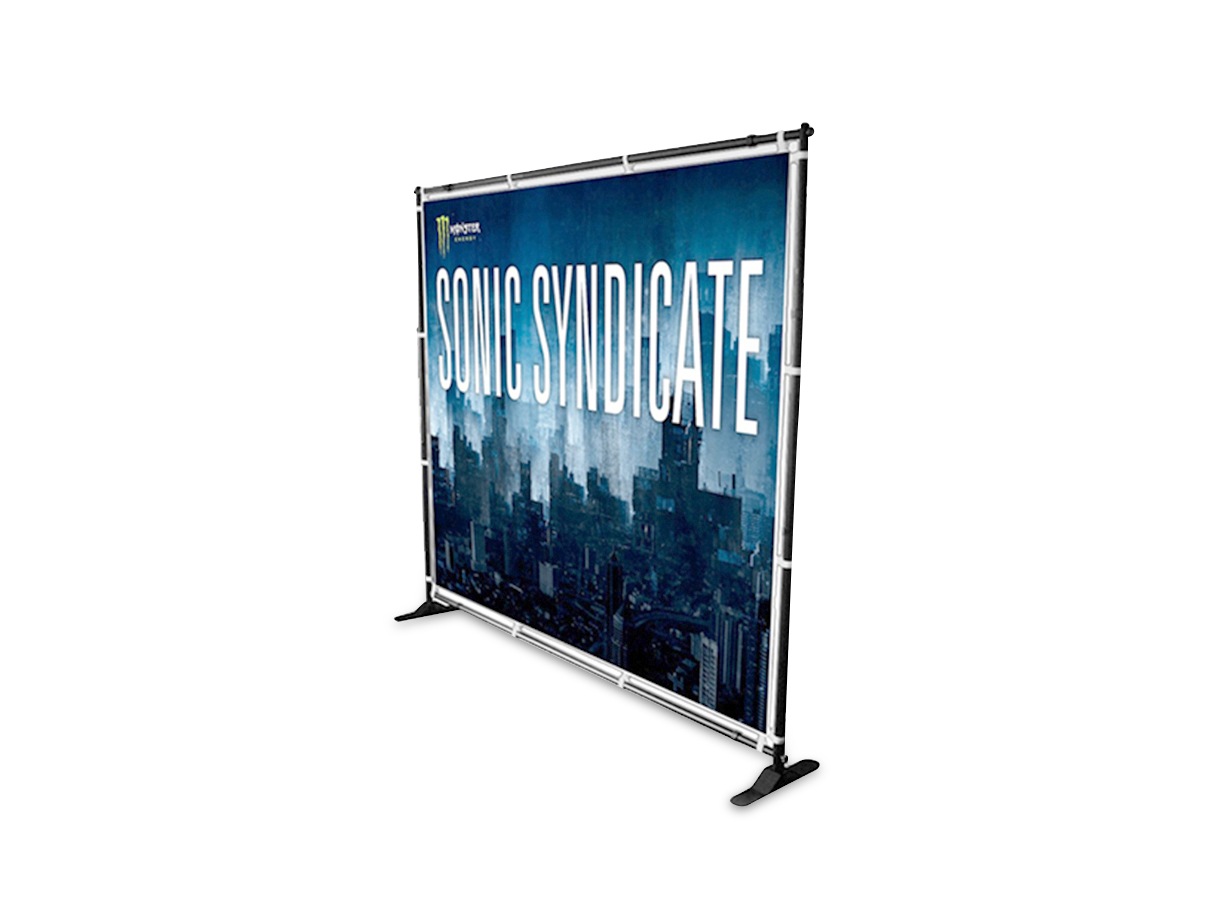
The extension of the failing spring is denoted u 1. Consider the three springs in the figure below.Ī three-spring system. Some springs are purely elastic and represent the undamaged material, while a certain spring fails. To understand this behavior, we can think of the material in the structure as connected springs. How can we mediate that we sometimes need to work with material models that do not fulfill the stability criterion? The important fact is that the material can be locally unstable, while the structure as such is still stable. For a linear elastic material, the requirement can be directly converted into the well-known requirements E>0 and \quad -1< \nu < 0.5. This is a condition that is generally computationally expensive to check for nonlinear materials. The discretized form used in finite element analysis implies that the constitutive matrix relating stress increments to strain increments must be positive definite in order for the material to be stable. This is called Drucker’s stability criterion or Hill’s stability criterion.
